Inverted machining is turning the industry upside down.
MODIG’s inverted machining centers set new standards in productivity, precision, and speed by processing from below.
With the world’s first inverted machines, MODIG transforms our thinking about generic five-axis part and component machining and sets a new standard for machining. The industry has been waiting for the next shift in performance after the CNC machines debuted during the ’60s and horizontal machining centers in the ’80s. Inverted machining means a new way of performance with the spindle machining from below.
Thinking new is not new to MODIG; it’s a continuation of MODIG’s decade-long technological leadership positioning and trend-setting machine tool designs. So, let’s think inverted!
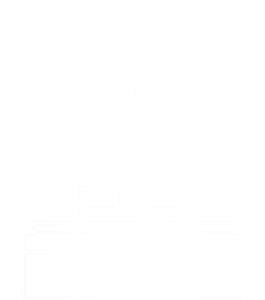
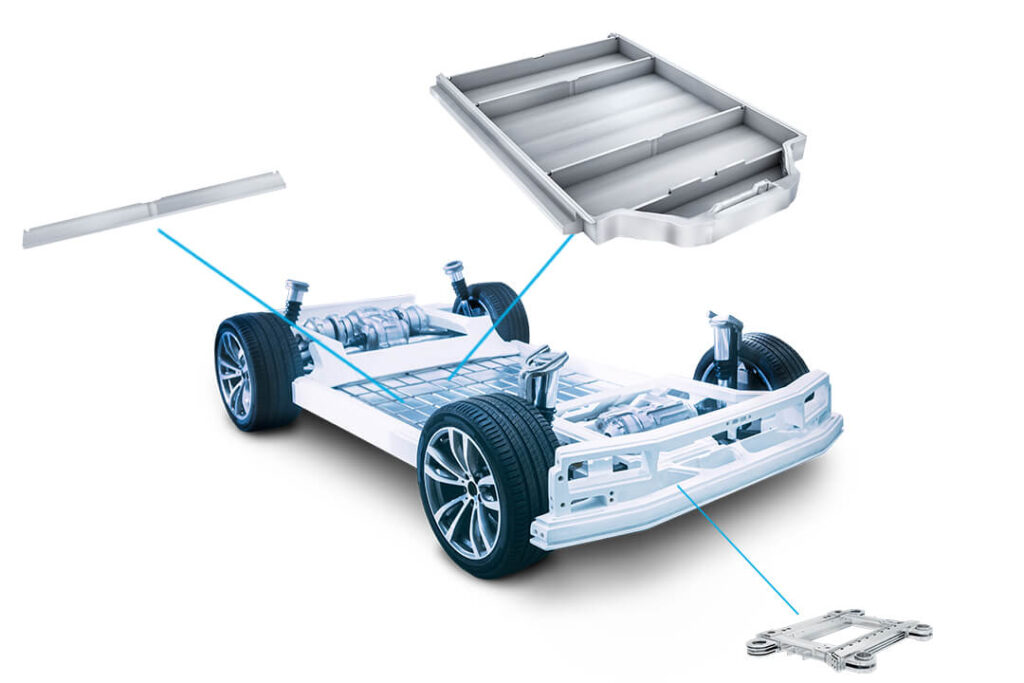
Automotive
Our machining solutions enable fast cut-to-cut times and add value to automotive part manufacturers. They are ideal for components with high complexity and large volumes, including engine cases.
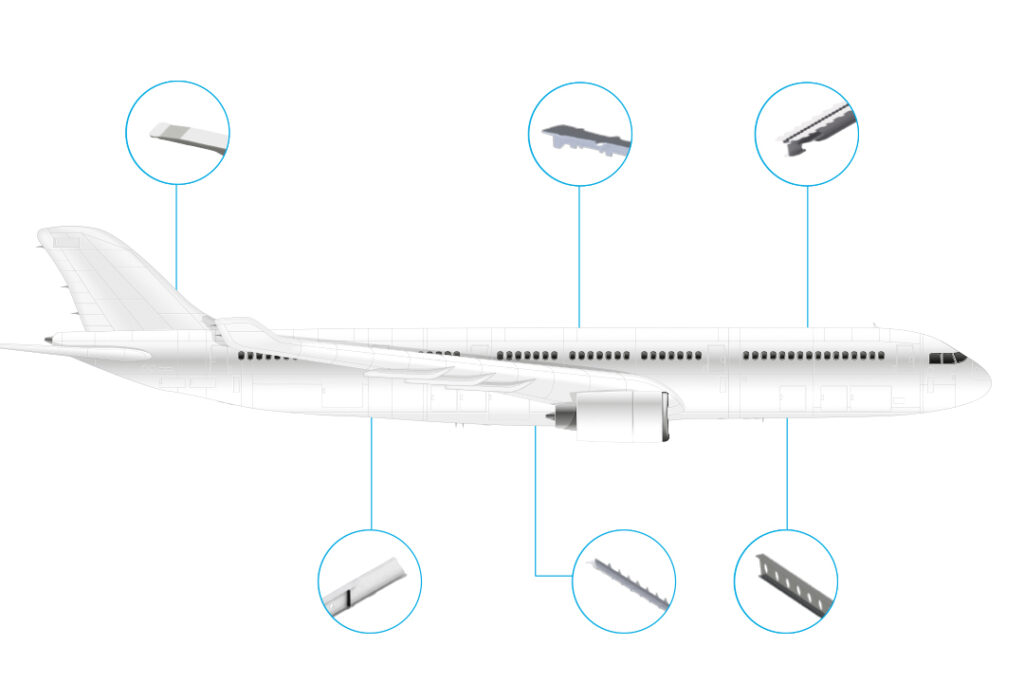
Aerospace
Find your machining solution for aerospace parts manufacturing. Our aerospace machining solutions improve productivity, precision, and cost-effectiveness, providing a competitive edge.
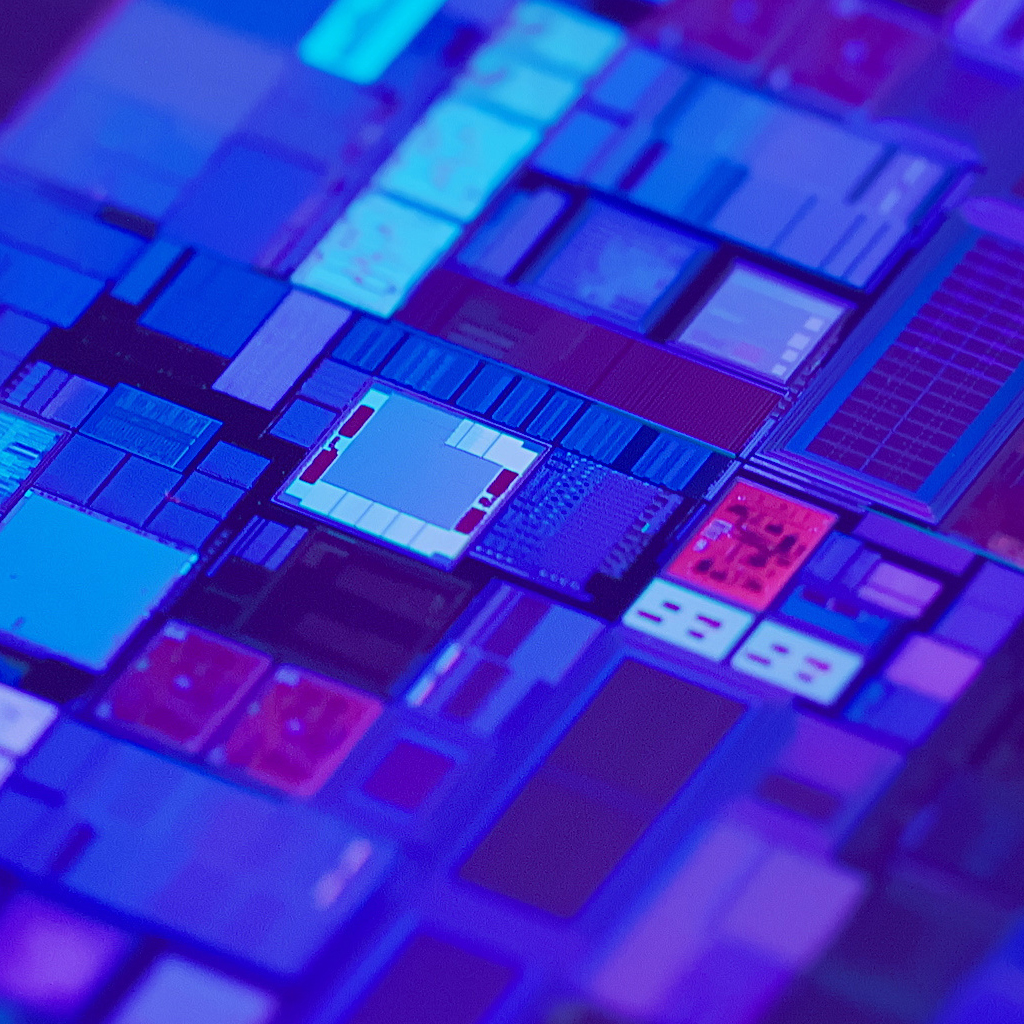
Semiconductor
We offer precise machining solutions for the semiconductor industry, ensuring minimum tolerance on flatness, surface finish, and dimensional precision of semiconductor components.
Inverted Machining Centers
MODIG proudly presents the IM range: customized machining solutions processing from below, with a wide range of design options and features, including:
- High-torque and high-power options.
- 4- or 5 axis.
- Inverted trunnion tables in multiple sizes.
- Optional mill-turn.
- Automation options including a pallet system and overhead mill turn.
- Suitable for cast iron, die casting, aluminum, titanium, composite, and steel.
- Industries: Aerospace, Automotive, Heavy equipment and more.
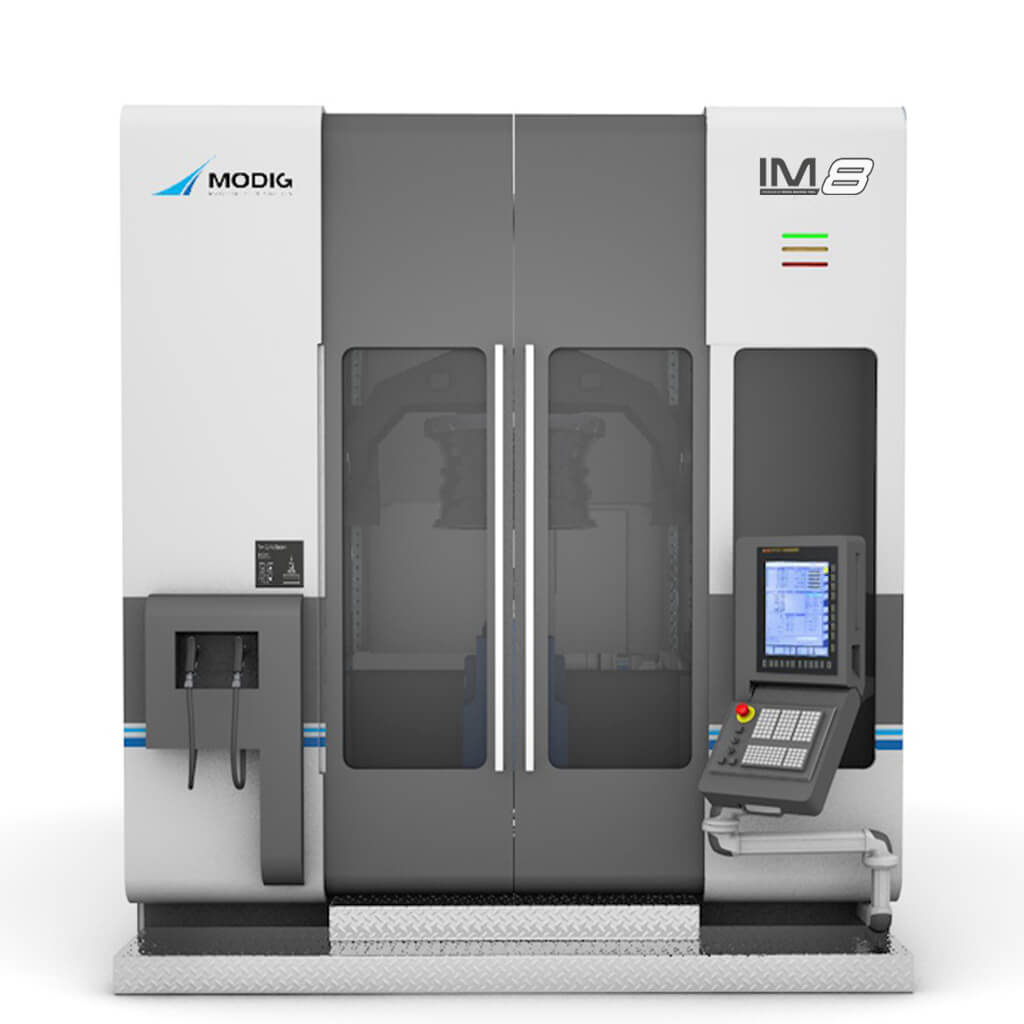
What is Inverted Machining?
An inverted machining center is a vertical machining center flipped upside down, with the spindle positioned to process materials from below. However, this brief description only begins to illustrate its capabilities. Inverted machining is an innovative manufacturing process that offers distinct advantages, including improved chip evacuation, enhanced accessibility to the workpiece, and heightened precision.
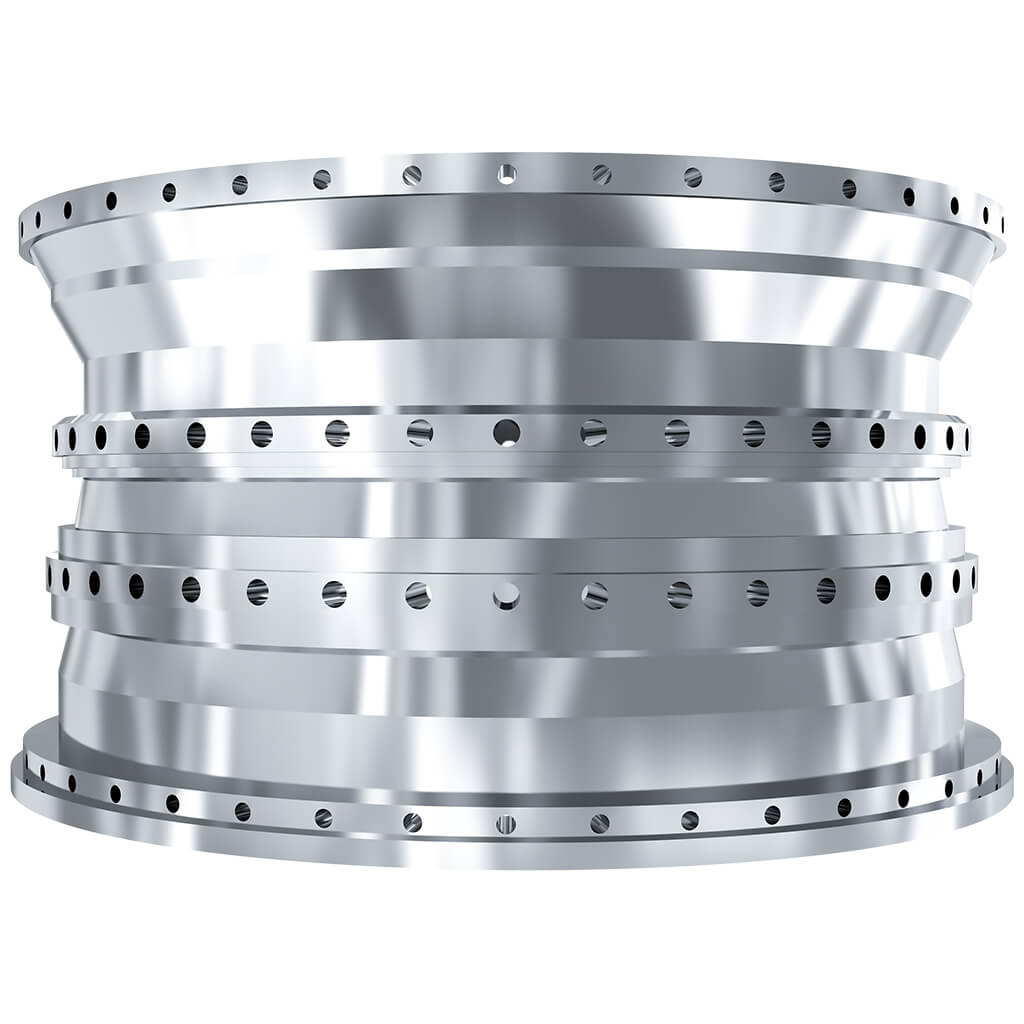
Increased demand for higher and higher tolerances
Today, everything from the body of a smartphone to an airplane is manufactured by machining. The complexity of these products and components is continually increasing. Traditional manufacturing methods for these products use vertical milling machines with a tool machining from above over a workpiece or horizontal milling machines where the device works from the side. But there is an increasing demand for higher and higher tolerance. To match these requests, there is a need for enhanced solutions.
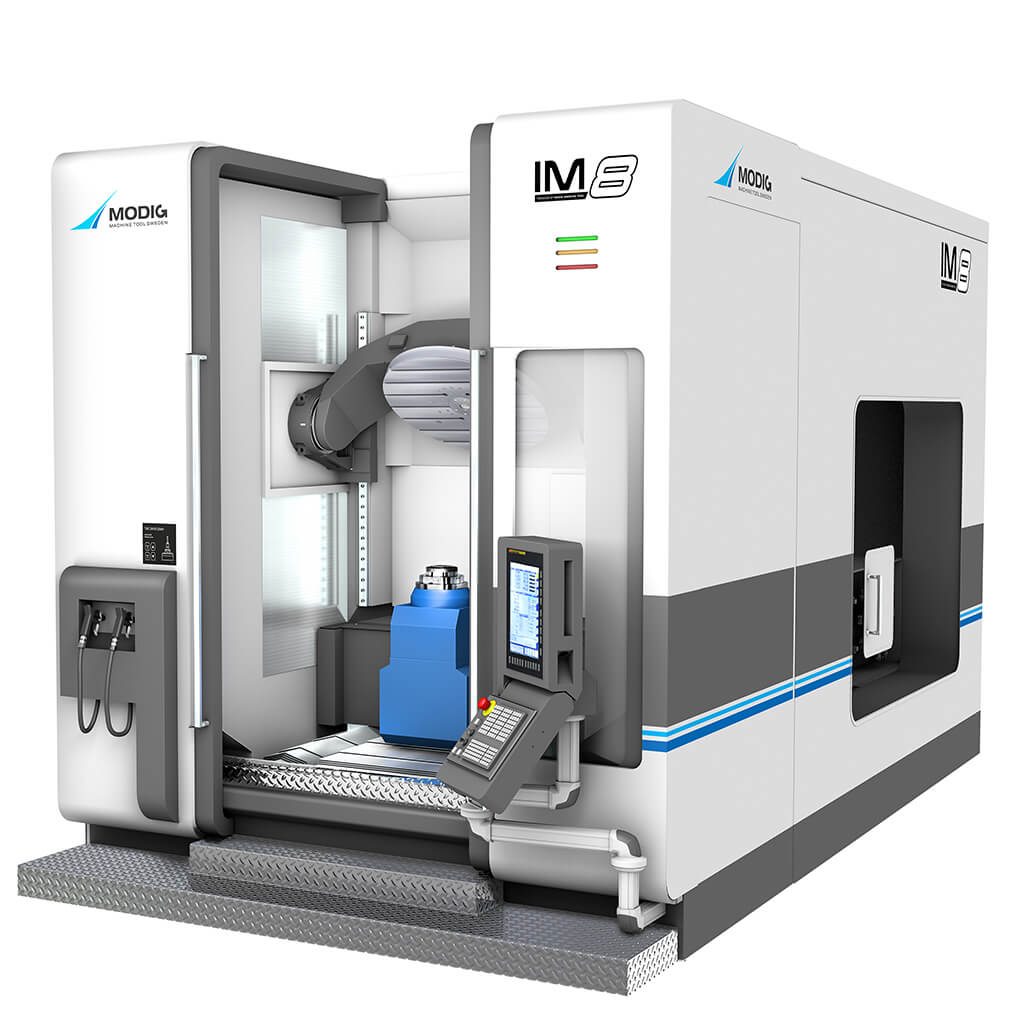
Inverted machining – The MODIG way
To meet the increasing need for improved machining solutions with higher speed and precision and improved handling of removed material, MODIG needed to think outside the box. After many simulations, it turned out that when the cutting tool was working from below, it was possible to effectively remove chips from the workpiece. Further, the design allows for a more stable machine, improving speed and precision.
With all its advantages over traditional processing methods, the machine with a spindle working from below was born. This is available with single or multi-spindle options. Discover our Inverted machining solutions
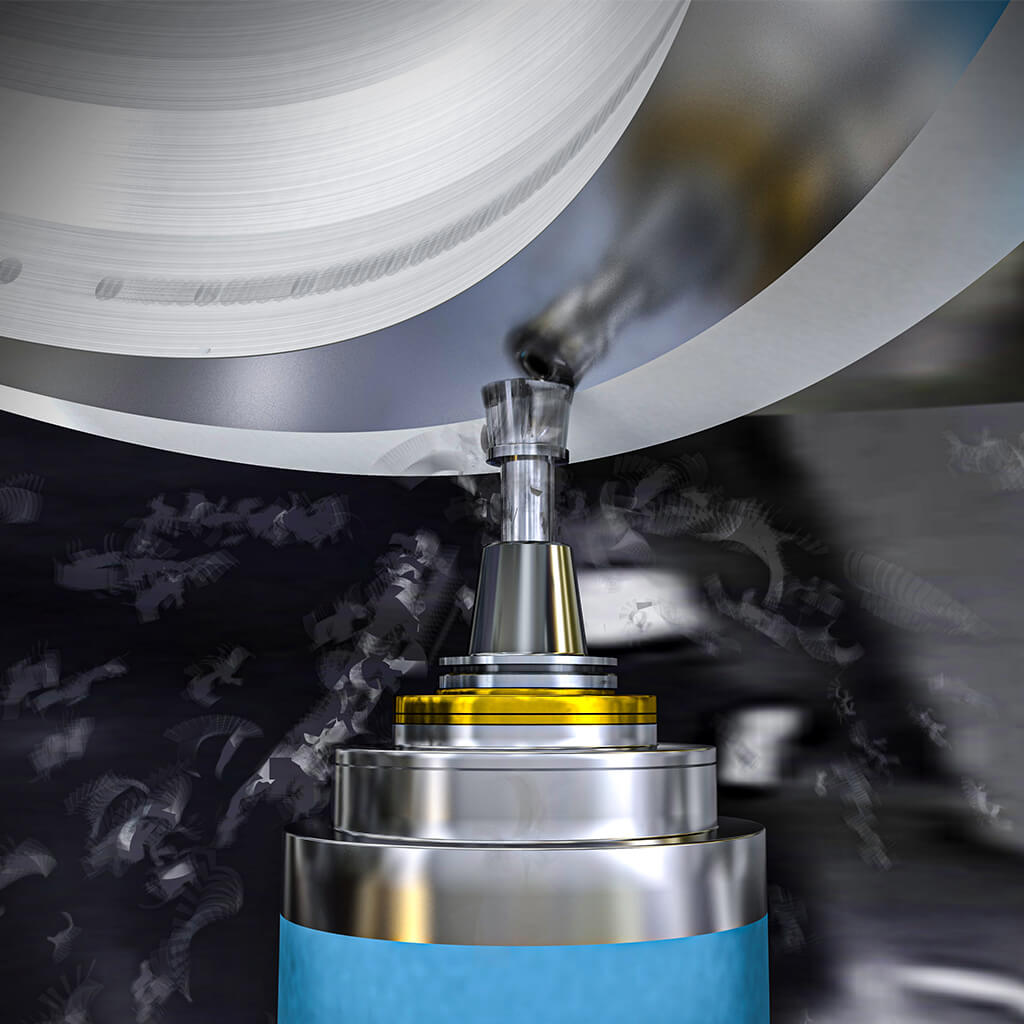
Why inverted machining?
Machining center processing from below offers several machining benefits over traditional processes. These include:
- Extremely rigid
- Optimal chip handling
- Incredibly fast cut to cut time
- Reduced footprint
Learn more about the advantages of inverted machining in the blog post Why Inverted Machining?
How Rigid Is an Inverted Machine?
In today’s production, we strive for even tighter tolerances and better precision, which requires stable and reliable processes. Based on this, MODIG created the inverted machining centers. With technical ingenuity and the ability to meet our customers’ needs, MODIG has built a stable machine with a cast iron base around the structure. Indeed, the construction makes the machine highly rigid and extremely fast—as well as a reduced footprint.
”Rigid, Inverted, Think Upside Down!”
For that reason, the engineers at MODIG have managed to separate the forces that occurred from the trunnion table’s vertical movement from the spindle’s horizontal directions to make the machine more stable. Doing this has reduced the side-to-side forces so that it does not affect performance, and the machine works with best-in-class precision.
Optimal Chip Handling with Inverted Machining Centers
How do you build a machine with an optimal chip-handling system?
This question has been a million-dollar question for machine builders throughout history. By turning the machining industry upside down and introducing inverted machining centers, MODIG is as close as possible to optimal chip handling today. Working inverted means easier chip evacuation with less consumption of coolant. The gravity makes the chips fall with a natural flow from the workpiece and the working area.
Turning the machine world upside down
For many machined components, there has been a problem with vertical and horizontal machining centers where chips fill up the work piece’s pockets and, after a while, the whole working area. Even if a horizontal approach creates more natural chip removal, the solution has not been perfect. Before, operators had to stop the machine for manual removal of chips. With machining centers processing from below, MODIG has set a new standard for chip handling.